We humans can move very heavy things, using just our brains and simple tools. Or hydraulics. For everything else, there are hydraulics.
One of the best ways of keeping machines from vibrating is to not worry overmuch about what they weigh. Make everything of steel, bolt it together with huge bolts, and let it be so heavy that it sinks into the concrete floor, slightly.
The guy I bought the grinder from loaded it into the back of my Chevy Tahoe using a forklift. He runs a business building high-performance tractors for tractor pulls, and had obtained the it for some unfulfilled purpose-or-other. I saw it on Craigslist and snapped it up. When the weight of the machine hit the back of the truck, the entire truck sighed and sank a couple of inches.
Steel weighs roughly 500lbs/cu ft. Which is 226kg per 30cm/cu. In those terms, the thing is positively “light and fluffy” since that would mean there is less than a cubic foot of steel, total, comprising it.
My patient neighbor with the bobcat (who helped me unload the forging press) [stderr] unloaded it onto my fine art shop dolly, and we pushed it down the hallway into the shop; he had to go do some Easter Sunday stuff, so I ended up staring at the thing for a while.
I sometimes describe people as a “FWATS” or a “FWAPT” (friend with a table ${table saw, pickup truck}) – but I convince myself it’s doing Mark a favor to start his bobcat every so often and make sure the tires are inflated and the hydraulics are working.
The grinder head moves up and down with the motor and drive assembly, and the table (with a magnetic chuck) goes back and forth with the work-piece, bringing it in contact wit the grinding wheel. Then, there are sparks. There isn’t much vibration because the machine’s legs are cast iron and the machine is heavy. I regret not photographing the leg-bolts (but I am never going to take them out; I will die with them in) – they are 1″/25mm machine bolts, 4 of them.
I actually wanted it to tilt when I raised it; that way I could get the leg on without having to haul it all the way up. As it worked out, I lifted it pretty high. The entire time I was near the machine, I was ready to maneuver rapidly backward.
I put the jackstand under the leg to raise it so I didn’t have to use one arm to hold the 100lb/45kg leg while I fitted the bolt. I also didn’t want any part of my body under the machine until it had its legs on.
Look at the power switch! When I got the machine, I borrowed some wire cutters and snipped the power wire (yellow) so that it would not work at all until I had a chance to re-wire it.
Do you see the razor blade hidden in the apple? I did!
Here’s the problem with the switch: it is positioned so that while you’re using it, your face is right where the work-piece is going to fly if you forgot to engage the magnetic chuck and the grinder wheel is in contact. Zwipp! Ow! I cut the wire and I’m going to mount a nice new emergency-paddle style switch on the front leg. And maybe a switch that is not full of dust and junk (the old one, open, is in the path of the cloud of ground steel coming off the wheel)
I spent about 2 hours with a paintbrush and some Gum Out engine cleaner, and – other than chipped paint – it looks like new, now. All the rust came right off with Gum Out and steel wool and a roll of paper towels.
This was all sort of a mental dry run for the real equipment move, which comes next monday. Literally, while I was driving down to do the transaction on the grinder, someone listed a Bridgeport knee mill on craigslist – 100 miles north of my house, while I was 100 miles south of my house, near Pittsburgh. The price on the mill was so embarrassingly low I asked the seller, “do you mean $1,100 or $11,000?” The seller said he’d sell the machine to the first person who put the money in his hand so I decided that I was going to piss my girlfriend off by screwing up our weekend, and got up at 5am, drove 220 miles to close the deal on the mill, then drove back to Pittsburgh so we could spend the rest of the day and evening together. Screwing up a dinner and computer gaming date is serious business, and I can’t think of the last time I did anything like that, deliberately. But that’s a ludicrous price for a working Bridgeport mill. It even came with what is easily $500 worth of collets and mills.
I’ll post the tale of that adventure if everyone (and the mill) survives. Since I know some of you are expecting catastrophe: so am I. I’ve been researching how to take the table off a Bridgeport (it’ll need to be off to fit it in the door, and it’s less likely to get damaged) and watching a lot of “how to” on field disassembly of the machines. I’ve gotten (“some assembly required!”) an engine hoist and a rental truck with a lift-gate, pry bars, truckers’ ratchet-straps, moving blankets, t-nuts and eye-bolts for the table. This is going to be a memorable project, hopefully in a good way.
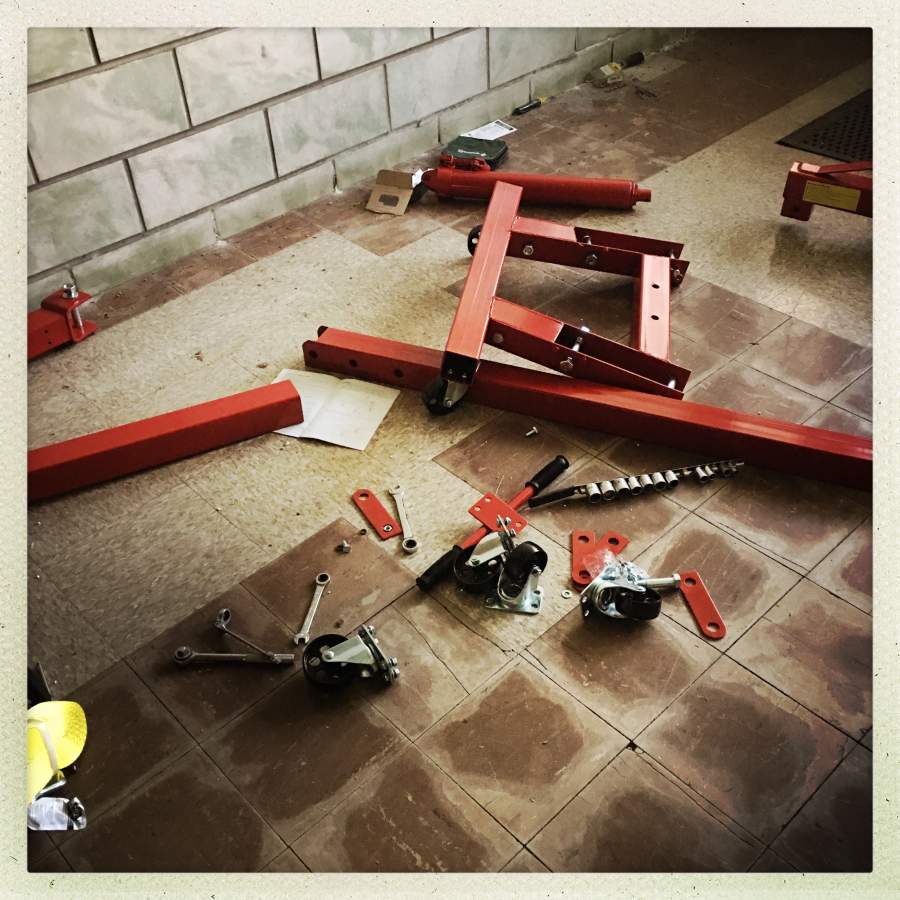
“some assembly required”
I have also put word out on the local whisper network (i.e.: my neighbor Bob) that I am going to be looking for an experienced machinist who’ll be willing to come check out my set-up, check the machine out for safety, and teach me how to trim and straighten the edges of my billet-bars, and fly-cut surfaces. I’m terrified of great big machines but I have been deriving a sort of law: big static machines are probably safer than lighter portable ones. A table saw is dangerous, but not as bad as a portable circular saw. Surface grinding a billet on my belt sander is much more dangerous and time-consuming than doing it on the surface grinder, because the controls on the surface grinder are two feet from the wheel and with a belt sander you’re holding the work-piece up against an 80-grit belt using your thumb-meat.
Today, the trucking company delivered the steel I ordered to make the sandbox around the base of the forge. Or, they tried to. The guy showed up with the semi-trailer and handed me a small box that only weighed about 60lb/30kg. “Is there a 230-lb 4 foot by 8 foot sheet of steel back there?” I asked the guy (I used English measures because 230lb sounds a lot heavier than 100kg!) It turns out the trucking company didn’t load it, or something, and it’s lost or sitting on a loading dock somewhere. I’ve got my hands full right now, anyhow.
I’m glad you’re graduating to a hydraulic crane instead of one of those evil pull-along winches. I dropped quite a few loads trying to hasten the ratchet action on a hand winch thingy when I was a lad. A 1 ton chain hoist was a much better tool for raising and lowering heavy lumps.
While I’m usually unable to appreciate photography I do like the picture of the hanging press for some reason. The slant of the press gives a good impression of the weight involved and yet there is a stark contrast due to the seemingly “flimsy” cable holding it up in the air.
komarov@#2:
The slant of the press gives a good impression of the weight involved and yet there is a stark contrast due to the seemingly “flimsy” cable holding it up in the air.
I’ve done woodworking most of my life, so I’ve got a pretty good sense of the lightness of wood, and its suitability for some things. So, when you start working with metal and industrial machines, it’s pretty cool – a little bit of steel is very very strong indeed. And very heavy. That’s a 5-ton rated cable. With engineering overhead it could possibly take 7-10 tons. And it’s the thickness of a pencil.
Then, you get to stuff like the drag line cable (wire rope) for strip mines. That’s 3/4 swaged high carbon steel and it weighs a lot per foot. I have no idea how much weight something like that can support, but engineers probably have it documented somewhere. A wood fiber rope of comparable dimension would weigh next to nothing in comparison and is as nothing in terms of load capacity. If you look at the picture of the surface grinder on its feet you can see my 100′ roll of wire rope on the floor to its left. The roll weighs about 170lb.
Lofty@#1:
I’m glad you’re graduating to a hydraulic crane instead of one of those evil pull-along winches.
I have been reading a lot of “how I dropped my milling machine” stories. Generally it sounds like the engine hoist is the way to go unless you have a back hoe handy.
Lifting stuff with back hoes: back around 2005 I managed to bury one of the wheels of my tractor in a mud-zone, up to the hub. So it was sitting there at a crazy scary angle and I had no idea what to do – so I called Bob who came up with a back hoe and snatched it out of the mud puddle like it was a toy.
I was talking to a guy up in my neighborhood (the guy who tows semitrailers out of ditches) (who was not interested in moving my wee little milling machine) he said he saw a fellow with a great big CNC machine in a truck, and the CNC machine shifted; then, the truck apparently continued on the road for a ways, on two wheels, before it fell on its side and the CNC machine exited the bottom of the wreckage. Everything suffered about $30,000 in damage.
Lots of people enthusiastically telling me stories about people getting mangled or spending a lot of money trying to move milling machines!
I am glad you are thinking this through carefully and using the right kit, but please make sure you stop when you get tired. Pushing to finish a job like that when you are tired is a great way to have an accident.
*** GORY STUFF ***
I’ve a friend who now only has 1cm of index finger and no nail on her middle finger (because she lost the top bit of that finger) because she made the mistake of cutting one last piece of wood with a table mounted circular saw when she was tired, and hit a knot. She isn’t a careless person, she was just too tired to react quickly enough. She was relatively lucky as the nearest hospital was in Sheffield and they have a lot of experience repairing that kind of injury otherwise she’d have likely lost more of the middle finger and some of the third finger. She also used the accident as an opportunity to move to a small holding and has ended up very happy, but still …
Somewhat off topic but related to steel cable…
I once visited the powerhouse for the San Francisco cable cars. They have an amazing setup there for maintaining the cables (which of course wear out regularly). They can splice in a new cable (or replace a damaged section) in real time — there’s a spooling setup that allows the cable in the street to keep running for a while as they make the splice, which is done without any increase in the cable cross-section. Once the new cable runs out and back, they do the same thing again to complete the new loop.
I don’t recall if they mentioned how much of the power goes to the friction of the cable in the ground, compared with the actual load of the trolleys.
As you possibly know, Hardinge bought Bridgeport some years ago. The Morris Group has the service rights (parts, docs) to Hardinge and Bridgeport products. Go here for parts and diagrams/manuals: http://www.morrisgreatlakes.com/home/customer_service/parts/hardinge_parts.html, Morris Great Lakes handles western PA.
One of the contractors I work with also does contract work for Morris South in North and South Carolina and is a big Bridgeport fan, he’s the person they always call for Bridgeport work, so if you need advice you can’t get from the reps let me know. You should also get signed on to the Practical Machinist/CNCZone forums which has amazing archives of machinist maintenance and operation comment threads. Have fun!
DonDueed@#6:
I once visited the powerhouse for the San Francisco cable cars.
Highly recommended place to visit! The set-up there is quite fantastic, with those gigantic cast wheels silently carrying the cable. I also wondered how much friction the overall system was dealing with. Probably not that bad, really.
San Francisco’s cable cars are a real delight for me. Last time I was there in a tourist capacity, my travelling companion and I went out of our way to go everywhere on the cable cars.
jazzlet@#5:
Pushing to finish a job like that when you are tired is a great way to have an accident.
Yes – you gotta know when to hold, know when to fold, know when to walk away, and know when to run.