The earliest adhesives appear to be plant resins (also known as “tree sap”), crushed and allowed to cure as the moisture evaporates out. Such glues are surprisingly good, since they’re basically doing what they evolved to do: congeal and hold things together. According to the internets there are glues dating back to 70,000BCE, which consist of powdered stone (ochre) mixed with resin.
I’m going to hazard a guess and say that if a glue outlasted the dawn of civilization and manufactured weapons, it was probably good enough. In terms of testing, there’s no test that’s as good as the test of time.
When I started studying photography in the early 90s (evening classes as Maryland Institute College of Art) we were studying in a program that aligned closely with the history of art in general. The first lecture(s) were about archival processing. Since we were doing chemistry-based imaging, archival processing was a big deal – especially since photography inevitably wound up on a wall for comparison next to painting. Painting goes way back to cave days, but the modern approach to painting would be familiar to the great artists of yore: linseed oil, pigment powder, plaster, clay – all of which are processes that have stood the test of time. I’ll note that there are probably a few masterpieces lost to us because some painter experimented with pigments, and their masterpiece eventually grew mold, or peeled off the board it was on, or mice ate it. But photography also had a dark history of chemical stains eventually appearing on prints, or metallic pigments oxidizing chemically, etc. The point of all of this is that I had it drummed into me that you have to constantly challenge your process and whether your work of creativity will stand the test of time.
That’s why I get a pained expression when I see some internet knife-maker on youtube do something clever like use a few drops of cyanoacrylate to hold a bigger glob of epoxy in place while it cures. Has he checked to see whether the chemistry of the one interferes with the other? Or, is he just putting something together because he’s not trying to make a knife that will out-last King Tutankhamen’s? Speaking of which, does that tang appear to be a bit loose? Maybe hide glue doesn’t hold up through a good afterlife?
By the way, King Tutankhamen’s knife was clearly not very good. Look at those sloppy grind-lines. But more importantly, it was made of meteoric iron, which means it probably couldn’t hold an edge if you, um, epoxied one on.
So, the first thing you have to do when you’re thinking of gluing something is ask yourself how long you expect it to be stuck together. And, if your answer is “70,000 years give or take” then you would construct the knife above using no adhesives at all, favoring a disk guard and disk pommel with a tang that goes out the back of the pommel and is peened down. Nowadays it might be threaded with an allen bolt made of titanium, but you get the idea. Once you’ve decided how long the thing needs to hold together, you can consider your materials. Steel blades can be roughened with a grinder to give them some “tooth” for epoxy to set in, must be cleaned of oil and oily fingerprints, etc. Then, you can glue surfaces that otherwise might not make sense, e.g: glass to metal. If you want to be crazy you can micro-etch the steel with a dunk in phosophoric acid to produce micro-pores for the glue. There is a whole beautiful art-form involving gluing glass with water-clear ultraviolet-setting polymers. Think about the physics for a bit and ponder how well ultraviolet goes through glass. Is the glue in the center of the glass piece fully cured, and how do we know? I’m not saying this will happen, but you do not want your beautiful art to spontaneously disassemble in a mere 2,000 years.
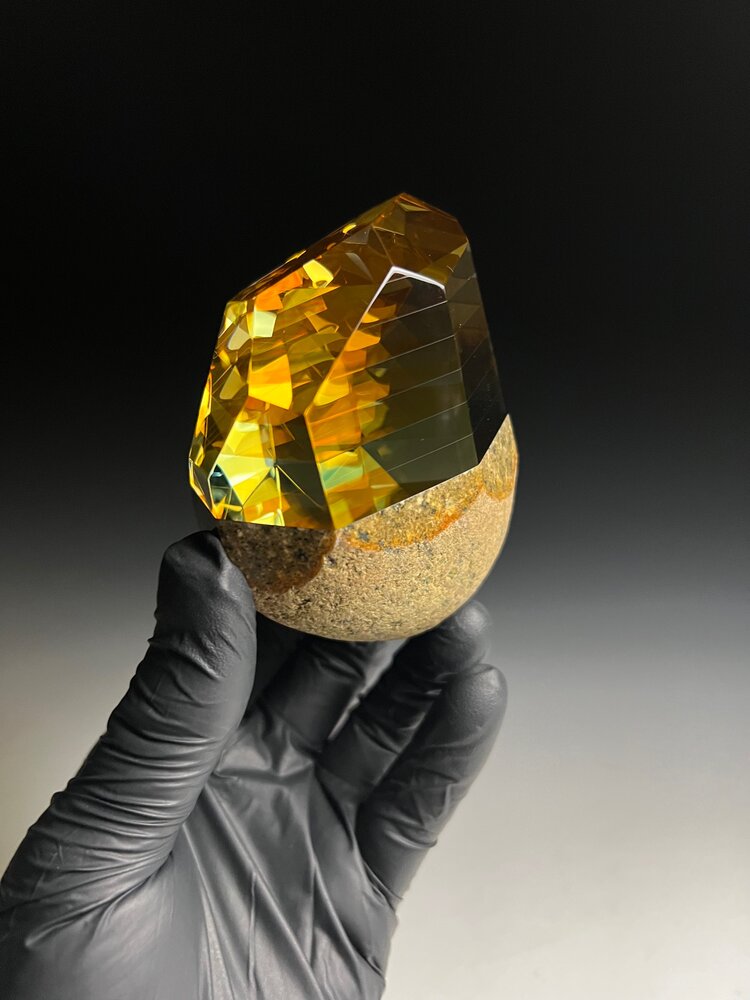
Art by the amazing Weston Lambert. I love this stuff!
So, you’ve got surface preparation. Sometimes you amplify the grip of your glue by creating a vacuum between the surfaces – a vacuum full of glue. That prevents your glue from oxidizing or getting wet, except for a tiny bit around the edges. It’s that tiny bit around the edges that sometimes turns into spontaneous disassembly hundreds of years later. The vacuum can be created the old school way: put something heavy on it. Or the new old school way: clamps! Or the new new school way: a silicone bag and a vacuum pump.
Where I get stuck is with compatibility. Back in the early 00s’ I took a class on mold-making at Smooth-On Plastics out in Bethlehem PA. It was a great course and if you’re inclined, I recommend it. One of the things that I learned, which had not occurred to me before, is that some glues (silicones and polyurethanes) cure through a catalytic reaction. I.e.: silicone hardens in the presence of a catalyst containing alcohol and platinum, or tin. Some polyurethanes contain coloring agents that interfere with that catalytic reaction in silicones, so you can’t even have them close to eachother, or the silicone may “un-cure” back into goo a few weeks later. How cool! Unless you made pharoah’s knife with a silicone handle and it turns to goo and you wind up flayed alive as an example to other knifemakers. I asked one of their material science guys and he looked at me like I was ignorant (which I was) and said, “some reactions catalyze at different speeds, so the curing reaction happens in 6 hours and the un-curing reaction happens in weeks.” The point of all this is you need to read the manual for your glues very carefully especially the sections about compatibility. And, remember, the manuals were written by materials scientists who are not kidding when they say “will not fully cure in the presence of alcohol” or whatever. There’s a universe of pain hidden behind every recommendation in the manual.
After compatibility, you’ve got to think of the archival nature of your materials. If you have a knife with a stacked leather handle and a stainless steel blade, you’re not looking at a knife that’s designed to exist happily at sea. Salt water loves leather! You can soak it in linseed oil until you’ve cornered the market on linseed oil, but the sea is a land of vibration, salt, electrochemical reactions (now that boats are not made of wood) and temperature changes. I will not try to make a knife for use at sea. “Go buy a stainless steel skeletal grip knife from Spyderco and be done with it.” Also, who hasn’t dropped a knife overboard? You need to think of these things. That’s why my handles are generally soaked in lots of layers of linseed oil and I avoid fancy polyurethanes and whatnot. I have no idea if they will last, but we know for a fact that linseed oil-soaked stuff can last 1,000 years or more. [By the way, if you’re making a knife intended to last 70,000 years, consider turning a handle out of motherfuckin’ granite on a metal lathe. Without wearing granite chips in your face, btw. Now I want to do a collaboration with Weston Lambert] A stainless blade, a granite handle, and fill the gap between the tang and handle with chopped carbon fiber and JB weld and you’re probably looking at a knife that will still be stabby in 70,000 years. Even if it’s buried under the supports of a Japanese temple, as they like to do. [sci]
Let’s consider that example a bit more closely. Granite. We know it wears like rock, because it’s rock. Carbon fiber? That’s trickier. Well, carbon is interesting because it loves to stick to other molecules but it’s dimensionally stable, not very reactive once it’s stuck, and it’s pretty much heat-proof. So we don’t need to look beyond the physics of carbon fiber to know it’s archival. [I expect some physicist on here to tell me I am wrong] What about the JB Weld? First off, it’s not exposed to anything except at the transitions, so anything that eats JB Weld will have to do it slowly and carefully – that’s why you want to avoid big gaps. But, if my stainless blade had a long tang and I threaded the end, then put tapped impact disk on the pommel, it’d be entirely mechanically held together and I don’t need to JB Weld, at all. See what I’m saying? That’s probably another reason I don’t want to make a nautical knife: it’d weigh so much the boat would tilt when someone lugged it on board.
I’ll say one last thing about mechanical assembly: Japanese swords.
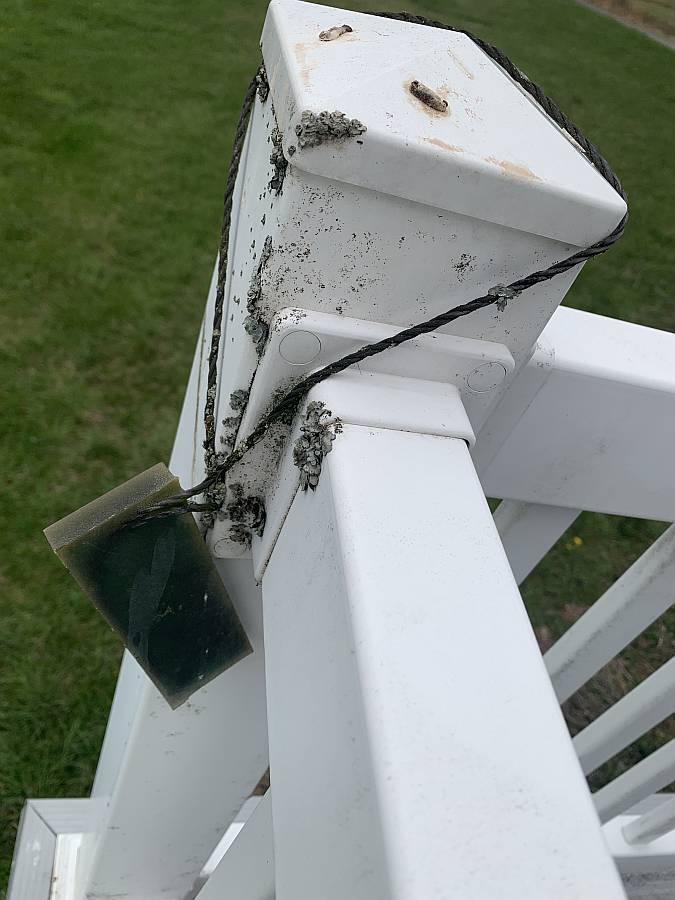
Epoxy resin with black pigment, cast-in carbon fiber rope, hung on my porch in the sun for 5 years, now looks like poo
I’ve had ongoing conversations with internet knifemakers, that starts like:
Me: Why don’t you cast one of those handle slabs you’re using, and tie it in a sunny place out in the weather for a couple years and see how it holds up?
Them: LOL
Somewhere, an old Egyptian knifemaker (one of the ones who didn’t get flayed alive) is nodding his tree-sap stained head.
I’m still on the fence about JB Weld and PC-7. There are things I made in high school that are still held together with PC-7. But will it last 70,000 years? Maybe. I don’t know. What I do know is that PC-7 and JB Weld are both instances of “steel filled epoxy” which is: steel and epoxy, with an amount of steel filler that controls whether it’s a liquid or a paste. I do know it is tough and lasts at least 40 years. I know people who have done things like cleaned out a cross-threaded screw-hole using a drill, making a nice clean surface, then packed the hole with JB Weld, let it cure, drilled and tapped it, and that fender is still stuck on that classic car like it’s bolted there. Again: the nature of that fix is such that there’s not a lot of oxygen, water, solvent, or ultraviolet light that can interact with the glue.
I tend to favor marine resins, though they are often “oh my god” expensive. Like West System G-Flex. [I am not taking ad dollars for this or any other posting] In those cases I am leveraging West Systems’ material scientists who do a lot of testing on materials to make sure they can survive in a nautical environment. And testing is expensive and time-consuming. Literally, time-consuming because there is no way to accelerate the effect of time and ultraviolet. This is a serious issue: there are entire generations of photographs that are currently crumbling because their surfaces were made with whizz-bang plastics and it turns out that outgassing from the plastic makes it crumbly over decades. Again, that’s why photographers who are crazy about archival processes like platinum prints on heavy rag paper – stuff that has so far outlasted the history of photography. I have sometimes been nearly moved to tears by the thought, “what if Michaelangelo had decided to use some newfangled pigment on the Sistine Chapel?” This is a serious issue: apparently Jackson Pollock (love his art or hate it) (I hate it) used to use random paints from the hardware store to make his great works – so curators are dealing with splashes of polyurethane atop latex on top of ceiling paint and dog knows what.
Another point about adhesives: use them sparingly! I see knifemakers who gob the adhesives in then clamp the heck out of their work until adhesives go squeezing out like a popped pimple. Don’t do that! Understand what you are gluing and whether a vacuum is an important part of it, and if it is, then make sure both sides of the work are thin-coated and there’s a vacuum fill where there needs to be. Then, assemble it so that bubbles don’t form. If bubbles are an issue, then consider a vacuum bag and pump system to degas your adhesive before you assemble it. This is a serious issue – PC7 can make a vacuum seal and there was one time I glued up the tang in a handle and left a great big bubble in the hole, which then forced the blade slowly out overnight. When I came down in the morning, the blade was 1/2″ out from the bolster. I had to hammer the handle apart and re-mount it. Most of the adhesives I use don’t expand as they cure with the exception of polyurethane (“gorilla”) glue, which is basically the same stuff as foaming insulation, just a different thickness. Foaming urethane glue can push your work-pieces apart. Make sure everything is thoroughly clamped.
One bane of a knifemaker is getting epoxy squeeze-out on the blade, then scraping it off and scratching the blade. Next thing you know you’re trying to mirror polish the ricasso without hurting the handle. This applies for woodworkers, too. (Machinists just thread and bolt stuff) (Welders just weld it and clean up the spatter with a flap disk) – if you’re going to have to worry about squeezout, put masking tape (motto: “it masks!”) on either side of the squeezout zone and peel the squeezout when it’s cured. Or, a fingertip-load of vaseline can be smeared onto the ricasso of the knife, because basically nothing sticks to vaseline. [Oh, and vaseline does not seem to have compatibility issues with anything] I have known knifemakers who would rather spend hours with a scalpel or chisel cleaning up glue rather than spend a minute slapping down masking tape or vaseline. [Masking tape is preferred for woodwork because vaseline can stain wood or, worse, prevent stain from taking once it’s in the grain of the wood]
I recommend not chasing every new adhesive that comes around. And understand what those adhesives are, so that you can make some predictions about their properties down the road. Frequently, I buy a tube of something-or-other and take it home so I can smell it. Not to get high, but to try to figure out what it is. For example, the silicone adhesive you can buy smells like ammonia – ah, no, that’s acetic acid. I’m not allergic to acetic acid, but I know someone who gets skin rash from it. Now, is that a permanent part of the adhesive, or will it evaporate as part of how it cures? I want to know these things, mostly because I’m curious. Or what’s that spray sealant stuff? I cured some and lit it on fire and it’s polyurethane. That’s fine, but I would not actually use the spray sealant to make my boat water-tight. You can learn a lot about compatibility by reading the label. And, did I mention that vaseline is pretty much compatible with almost everything? That’s why you are enjoined to use a smidge of acetone or denatured alcohol to get those oily fingerprints off your glue joint. I once saw a knifemaker eating fried chicken while he was doing a glue-up. It’ll be OK but it’s not as strong as it could be – fried chicken is more or less cooked in vaseline.
In the above picture, I’m getting a bit ahead of my self posting it, but it’s relevant. That’s the ferrule end of a wood lathe chisel I made for a student. The end of the chisel usually has a nice brass or copper ferrule to help absorb any shock on the blade, but also to make the handle do a “slowed down disintegration” if it’s deciding to come apart. Having the chisel-end of a chisel starting singing “freebird” while you’re using it is a Bad Thing. So, for these chisels I packed the tang hole with carbon fiber yarn and G-flex to bed the blade, then wrapped the ferrule end with more carbon fiber and G-flex. Then, I put a nice brass ferrule over top of all that carbon fiber. Carbon fiber is amazing stuff and as an experiment I took a piece of the yarn (shown above) and made a foot loop in it, hung it from a beam, and stepped up into it. It cheese-sliced my shoe sole but otherwise showed no sign of giving a fuck about anything in the world. So that’s about 2 yards of carbon fiber and a bunch of G-flex, adding lateral stability to the handle. Since I knew I was going to be smearing epoxy all over the place, and I was going to do a linseed oil and wax finish on the handle (G-flex will keep those from soaking into wood fibers) I wrapped the whole thing in shrink-wrap plastic to protect it from my grubby paws. That was effort well spent because I got G-flex all over the place.
I’ve put some thought into producing a decision tree that encapsulates my glue selection process, but it’s really simple.
- If woodworking for an indoor project and I want glue to fill gaps, use gorilla glue. Keep that stuff off the wood grain because it’ll interfere with any finish you attempt. Does not work well below freezing. Urethane glues are great if you’re going to put a protective coat of paint over top of them.
- If assembling something that needs to be tough, which will be away from UV and water, use G-flex. Why? It’s a lot easier to smear into position than PC-7 for darned sure. Does not work in cold environments; generally epoxies heat cure.
- For everything else, there’s JB Weld or PC-7. I consider them to be basically two different thicknesses of the same thing. I’ve never had PC-7 not stick, or fail. Once, in college (1983 or so) my motorcycle “the stinky ninja” was so called because the gas tank was weeping where there was a rust spot. I smeared PC-7 on it and it was still tight years later when I saw the guy I sold it to racing it at Summit Point. He totalled the bike, later, but I bet that PC-7 was still tight. It’s pretty amazing to be able to put glue onto a gasoline-coated surface (gas is basically thin vaseline) and have it stick.
- For things that need to be impact-safe, reinforce with bare carbon fiber yarn, coated with a thin layer of G-flex then wrapped really tight. Allow to cure then complete the construction. By the way, if you do this, get it right the first time because chopping apart carbon fiber yarn and epoxy is not even a little bit fun. It submits grudgingly to a diamond wheel on an angle grinder, but wear a particle mask because carbon fiber may turn out to be toxic some day.
- For acrylics (plexiglass, etc) I use solvent welding fluids, which basically create a thin layer of gooey molecules on both sides of the joint and when you push it together and the solvent evaporates out, it’s molecule-to-molecule welded.
- If you need a bulky join for acrylics, use acrylic glue.
- I’m not a fan of PVA glue, except for making slime with it. [And if you are going to do that, just buy PVA powder on Ebay and mix your own, which is way better! I was Central PA’s slime pusher for a while.]
- I have very little use for silicone glue except for when I am assembling something I may want to disassemble later. It’s good for that. I’m not being snarky – sometimes materials are expensive and you want to be able to reclaim them if a project does not work out.
Always remember the chemical properties of your adhesives! For example, silicone is great for making fish tanks but because of the acetic acid, please don’t put fish in right away! I realize as I write this, fire resistance is another topic I did not touch on. Generally, if you need fire resistant adhesion: weld it. If you can’t weld it, thread it and bolt it.
Oh, one more thing for the nerdy: inconel is crazy tough stuff! It’s iron/nickel/chrome steel and it’s what’s used for high-temperature applications that need to resist oxidizing and melting. Unfortunately, it’d godawful expensive, but that only makes sense. Many blacksmiths spend a lot of time replacing the bottoms of their forges because flux (borax) eats firebrick like I eat pizza. But, I made a 16ga inconel tray and now I laugh at the puny efforts of the flux. After 30 forge-welding heats, the tray has some smears on it but it’s intact and so is the floor of my forge. The thin inconel does not add significantly to the thermal mass of the forge, which is more than I can say for the great big hard firebricks a lot of blacksmiths use to soak up flux. I actually went around calling the engineers at a couple companies that make forges to tell them to offer inconel floors, but so far – nothing.
Nothing to say other than cool stuff. Better than learning about all these things by trial and error myself.
*blinks*
-Why- do you have a poop block carbon fiber soap-onna-rope thingy?
seachange@#2:
-Why- do you have a poop block carbon fiber soap-onna-rope thingy?
I made it as a test object so I could see how it held up to weather, freeze/heat cycles, sun, rain, etc. I was also curious how carbon fiber yarn would hold up. The carbon fiber looks pretty good but I wouldn’t use that particular resin for a knife handle unless it was just going to hang on a wall somewhere.
I probably should hop in my time machine and set up a similar block with some West System boat resin, but Barack Obama has the keys to it and I can’t seem to get him to bring it back because he keeps saying that he did, I’m just in the wrong timestream, or wossname.
All organic materials (like plastics) are susceptible to degradation by ultraviolet light, x-rays and other higher energy radiation. In general, thermosets (with cross-links between the chains) can withstand it better than thermoplastics. Adding fillers, pigments or radical scavengers can slow down that damage to a certain degree. However, there are chemicals that eat basically any plastic for breakfast. Luckily, those are not things we usually encounter in our daily lives.
Which adhesive to use depends very much on the substrate. In my daily work I prefer epoxy adhesives. Although modern acrylic adhesives are also very good and generally are less picky w.r.t. surface preparation. They also work well on stainless steel.
For cutting carbon/epoxy composite, it is best to use diamond coated burrs or disks. Those cut through composite like butter. The rotational speed needs to be really high, like north of 20k rpm for a 6 mm tool. There are basically two kinds. You have small “grit” of industry diamond embedded in a layer of e.g. nickel on a steel shank. And you have the thin-film vapour deposited diamond coatings on cemented carbine tools. Those are more for professional use and much more expensive but can last a lot longer.
You have to be careful when combining carbon/epoxy and metal. In the presence of water galvanic corrosion can occur very fast. I’ve seen wet carbon fabric etching a mark in an aluminium mold in less than an hour.
And yes, carbon fiber composite is very strong, if the fibers are aligned with the load. For example, woven carbon fabric with epoxy can have a tensile strength of over 1000 MPa in the fiber directions. The yield strength of basic construction steel is in the order of 230 MPa. The compression strength of carbon/epoxy is only about 50-60% of the tensile strength though.
I don’t remember where I read this (maybe Wikipedia, but I am too lazy to look that up now :-)). It seems that the original formulations of silicone glues released hydrochloric acid when curing. If I recall correctly, industrial silicones still use that chemistry, but consumer-grade silicone has a modified chemistry to release acetic acid when curing (less harmful, for sure!) at the cost of a longer curing time.
I make kitchen knives with carbon steel and wood, someone will destroy them by sticking them in the dishwasher well before the glue fails.
On the other hand that’s a persuasive argument for doing mechanical assembly on the knife set I’m planning.
On timescales exceeding human lifetimes (or civilizations?), I wonder if the steel filler in JB weld and similar epoxies would be a liability. I’m under the impression that most (all?) plastics are somewhat porous(?) to gasses, and am assuming the same might apply to epoxy? so over a long enough time span, all of that steel may get oxidized by atmospheric oxygen gradually permeating through the epoxy. And rust is bigger than iron – also an issue in a lot of reinforced concrete (which I also sometimes wonder about the lifespan…), where it will sometimes start spalling and cracking because the reinforcing steel rusts and expands. For a situation like Marcus describes, with bonding two well machined pieces with a minimal amount of glue, and not much need to fill gaps, I wonder if a “plain” epoxy might be sufficient? But then, at that time scale, there wouldn’t be any blade left, so…
I’ve also heard of galvanic corrosion issues with carbon-fiber bicycle parts combined with metal ones, and not being properly protected/greased/anti-seized/whatever.
I wish the knife “community” wasn’t so saturated with magats and bigots. Now that I finally have a tiny bit of disposable income, I’ve been considering buying a handmade folder, or maybe even commissioning one, and I’ve been considering going to a knife show or similar, but don’t think I could stomach the general environment nowadays…
Don’t get me started on Gorilla _brand_ glue. Some years ago, when the stuff first came out, it was notorious for not working out of freshly-opened containers, even if the listed expiration date was a few years down the road.
OTOH, you can make hide glue out of gummi bears!
https://blog.lostartpress.com/?s=+hide+glue
fusilier, Neandertal wooddorker
James 2:24
I thought everyone knew that latex condoms do not hold up well when exposed to petroleum-based lubricants. This is why KY jelly was invented.
Here’s a surprise for you: NASA makes a high temperature alloy by 3d-printing oxygen into the structure.
I have sometimes been nearly moved to tears by the thought, “what if Michaelangelo had decided to use some newfangled pigment on the Sistine Chapel?”
His compatriot, Leonardo da Vinci, was known to experiment in this manner and some of his works are in terrible shape.
Fortunately, digitized images do not suffer from this problem, but they certainly do suffer from the issue of legacy media not being able to be read any more (8 or 5.25 floppies, anyone? Paper tape, maybe?). I know someone who collected a few hundred GB of scanned genealogical data on a sizable portable hard drive over the course of several years. Would be nice to transfer all of that to a little USB 3 stick or similar, but the drive has an “ancient” USB interface. I calculated it would take something like 20 hours to transfer everything. I am not even sure that the drive could run that long continuously without burning up. And that’s not what I would call seriously old technology.
The 90s was not long ago. Anyone remember SyJet drives or Zip drives or Bernoulli boxes?
There is, of course, the other type of permanence.
Consider the classic, sometimes still preferred, usually acceptable and effective Kay-bar knife in its original form. Common 1095 steel that rusts so fast in salt that you can watch it happen if not oiled. The leather washer grip and sheath that could rot in a week if you didn’t treat them. But they worked. In rare situations they could be made to last for years even around salt water. If you worked at it daily. Typical WW2 logistical planning was that they would be replaced every week or two. So frequently that most Marines never got around to sharpening one and finding out that the steel could be brought to an acceptable edge with a piece of random concrete.
I left one on the side of a cliff in Kentucky after using it as a field expedient piton. Thousands were left in and around war zones world-wide. I’ve owned about a dozen. Good solid, reliable knives. But my loyalty is to the form not any single blade. I’ve got one in my tool box. I take it out and give it some TLC with a stone, oil and Huberd’s shoe grease every year or so. Still makes the hairs jump off.
The modern version is usually stainless. They don’t rust much but you can’t take it from soup-spoon dull to acceptably sharp with a piece of brick or a random rock. The sheaths and grips are nylon or synthetic. They don’t rot or swell, but they can be slippery. Everything is compromise.
In 1095 steel and leather Kay-bars were only designed to last long enough. Optimized for the other end/ form of things that endure.
Zip-drives, for a while they were the shit. Not many around any more who have heard, or felt that sinking feeling after the ‘click of death’. Oh, the fun we had with IRQs. I’ll take the root canal instead if you please. Soldering tiny jumpers onto traces you had to scrape down to get a decent sound card to work on a Compaq PC. 8″ floppy disks. Windows on 27 individual 3.5″ floppies. Monochrome monitors. limited RAM. 8 Byte file names. Manually parking the heads on hard drives. It’s all different now. The things I’ve seen; the fun I’ve had.
@12:
8 Byte file names? Luxury!
I love your rabbit-hole writing.
Surface prep is an interesting industry (see e.g. the wikipedia article on “parts cleaning” for a gangly overview).
My understanding is that applying solvents to steel and wiping or blowing it dry is not effective if you want true or optimal glue/coating bonds. The reasons are various, but the two big ones are:
1) even if you put an entire steel part in an ultrasonic tumbler and let it vibe & slosh until the sun burns out, once you remove it and let it dry there’ll still be a thin layer of oil molecules stubbornly clinging to the metal (a microfilm). Oil is tenacious, and a layer of it will always be more strongly attracted to the metal than to moving into the solvent. This problem is solved industrially in many ways, but a common one is to use e.g. bleaching agents to chemically alter and/or decompose oils such that they don’t want to stick to metal anymore.
2) there is oil on your fingers, obviously, but also in most “clean” cotton rags, on your fresh pair of gloves if you’ve touched anything non-clean with them (e.g. a tool), in your breath, in your compressed air, floating around on/in dust in the open air, etc. Simply leaving a cleaned object lying around for a bit will see it acquire a brand-new oil microfilm from the air itself! This is less true of carefully-filtered air, and that’s its own fascinating rabbit-hole industry (i.e. industrial atmosphere control). This contamination problem is solved by being anal about cleanliness and/or by not cleaning with wetting processes in the first place (e.g. by sandblasting with clean and even sorptive media and purified gas).
You might appreciate Dan Gelbart’s old video about coatings & adhesives from his excellent Building Prototypes series:
https://www.youtube.com/watch?v=x7onZGqrYyY&list=PLSGA1wWSdWaTXNhz_YkoPADUUmF1L5x2F&index=6
(that link’s from the playlist of the whole series. he also has some neat videos from this decade: a shop tour, one on his historical tech curiosities, one on his scratch-built submicron-accuracy air-bearing lathe & grinder, and on his company’s deposition-style sintering 3D metal printers)
He’s the kind of person I want to be when I “grow up”, i.e. one that never lost their childhood curiosity. Fascinating guy with an long and interesting history. Started & sold various optics & film-based companies of his own, was at Eastman Kodak doing cool stuff, has all sorts of (legitimate, non-trollish) patents, is something of a polymath, etc (which is increasingly-rare as time goes on since all technical subjects are requiring ever-more specialization to understand).
Also, fwiw, there are such things as self-etching paints and adhesives, which tmk include industrial acids (sometimes even fancy engineered biomolecules) which chelate or otherwise chemically interact with metal surfaces and can thus make up to some degree for inadequate surface preparation. However, I think the main purpose of such products is to improve bonding on properly-prepared surfaces, not to overcome poor prep. It’s still best to just do prep as effectively as one can.
jimf@11 says:
“Fortunately, digitized images do not suffer from this problem, but they certainly do suffer from the issue of legacy media not being able to be read any more (8 or 5.25 floppies, anyone?”
Guess what holds those tiny magnetic particles to the thin plastic disc? Adhesives!
They noticeably fail over the course of a few years of use, but the 8″ and 5.25″ sizes, lacking rigid shells, would fail faster due to mechanical abuse.